[This is a long entry, but one we think will paint a rich picture of what we're learning.]
Monday: 19 January 2009: Khong Chiam, Ubon, Thailand
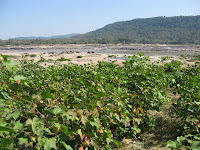
This week we will continue our visits with members of some of the groups that work with the
Pattanarak Foundation. Today we went to some women's homes. Last week, our study tour began with a visit to one couple's organic cotton field on the western bank of the Mekong River, where cotton, corn, vegetables and herbs are planted when the waters ebb as "cool" season begins.
We spent most of the rest of last week at a community learning centre, where a lively group of 7 women introduced us to their traditional production of cotton. They have perfected each step from the removal of the cotton seeds, to the fluffing, rolling and handspinning of the cotton yarns, which are then dyed with natural materials, dried and then re-wound several times to ready them for the loom. [Ellen will post a photo essay of this process when she gets access to a computer with the necessary software.]
The learning centre, built 2 years ago, is used primarily as a training centre for group members, local students and visitors from other weaving groups. It also houses a shop, where products are available for sale. Group members, like many women, work in their own homes surrounded by children and extended families, squeezing the work between their other responsibilities as mothers, wives, farmers, caregivers, etc.
Today we drive to a village of about 250 people who are primarily sustained by farming and fishing. The first home we go to doubles as a corner store. The woman here frequently rises fom her loom to sell a packet of washing powder or a bit of something else. In between customers, she returns to her weaving or to taking care of her children who, although small, appear old enough to be attending school but aren't.

The work on her loom is of particular interest to us because, unusually, both the warp and the weft are handspun. This means that the fabric she's producing is 100% organic, as well as thicker than the cloth produced from factory yarns. She is weaving with a 2-ply yarn so, when she is able to sit down, the work progresses quickly. She explains that she has not spun the yarns herself, despite the presence of 3 rustic spinning wheels nearby. Instead, she has bought the yarns from the village spinning group. "Baw mee waylaa wang," she shrugs, as she motions with her chin -- in the way people here do -- to the shop, the children and the house. "No time."
Aew, the Pattanarak field worker who is acting as our guide, asks the woman to bring out some already completed weaving, which is nothing like the white hand towels presently on the loom. We look through the pieces, which have an interesting mix of thick and thin yarns, designs resulting from both continuous and discontinuous supplementary warps and a choice of two colour palettes.
We choose 5 pieces that we will market as table runners. What a concept; what a contrast. There isn't a dining table in sight; only a cement sitting platform, covered with ceramic tiles, and little else.
The 3 of us continue our walkabout. Our next stop is at a tiny building of cement blocks, which have neither a skim coat of cement nor paint applied. What sticks in my mind, 6 hours later, are the battered and rusted pieces of corrugated roofing material that are nailed over the windows.
Outside, there are 2 young women and 2 very young children. One of the young women squats on the hard-packed dirt in from of the front door, while she winds soft green yarn onto bobbins with a spinning wheel of the type also used to spin cotton yarn. There is also a middle-aged woman, one of the women's mothers, we're told, standing by a well-used rice winnowing basket that contains several skeins of cotton yarns in 2 shades of green.
All of the yarns used in these villages are coloured with natural dyes made from locally gathered materials. The dyers pay particular attention to harvesting them sustainably to ensure a continued supply.
I take a closer look at the loom alongside the house. On it is a narrow warp of fine cotton yarn that has been spun in a factory. The thicker, handspun yarns are better suited to other types of weaving. I continue my inspection and count 20 sets of string heddles suspended from bamboo poles over the warp. "Photograph the heddles," I motion to Ellen, who always has her camera in hand. "They're fabulous."
We had been told in advance that this is a village where
khit (supplementary weft weaving) is done. In particular, this woman weaves the elephants that are used as a decorative motif on many of the bags we've seen at Pattanarak's shop in Khong Chiam. The complex string heddles shape the elephant design that she weaves.
While the young woman winds the bobbins, we go next door to pay our respects to Yai, the 83-year-old grandmother who, as a young woman, came across the river from Laos to marry, raise a family and eventually teach daughters and granddaughters how to artfully manipulate the string heddles. Bundles of these threads tied to bamboo splints hang from various houseposts in the compound. They are the inheritance of their Lao foremothers: the heddles that the grandaughters have the stamina and eyesight to use, but do not yet have the skill to tie for themselves.
We sit with Yai while Aew steps outside to answer her mobile phone. It's hard not to look away from the old woman's gaze as she speaks a steady stream of village-accented Lao. Her mouth is a red slash of crumbled teeth and blackened gums; her skin appears to be a deep hepatitic yellow. Tiny and wrinkled, she appears shrivelled into a pile of skin and bones on the cement floor. I pick up the occasional phrase, which I optimistically weave into a meaningful narrative. I tell Ellen that she might be saying that now that she is 83 years old she should be dead already, like her contemporaries, but she does not die. The betel chewing has ruined her teeth, but not her health apparently. [Betel - the leaves and nuts of a local tree - is chewed throughout Southeast Asia for its social and psychotropic qualities. Particularly common among older women, we see betel being chewed in every village in Thailand.] Likewise, the tumeric-infused oil has kept her skin pliable, if yellow. When Aew returns and we are able to take our leave, we back out of Yay's presence with silent but hopefully graceful
wais. [This is the gracious method of greeting and taking leave of people in Thailand and Laos, with hands brought together respectfully in front of you.]

We return to the loom next door to find the 2 young women working together; one is throwing the shuttle and the other is manipulating the bamboo sticks that control the string heddles, speeding up the work. In our 10-minute absence they have woven several rows of elephants, which they are now examining with Aew. The woman seated at the loom points out that the elephant on the far left of the piece is not quite like the others. It takes a practiced eye to spot the discrepency but clearly the weaver is not satisfied.
"Tomorrow," Aew translates, "she will have all of them pretty and she will begin to weave."
I understand that this means that some part of today will be spent correcting the strings responsible for the misshapen elephant, as well as winding the rest of the yarn onto bobbins, so that tomorrow the weaving can begin in earnest. I am reminded of a comment made several years ago by another weaver: "By the time you're ready to sit down at the loom to weave," she had said, "most of the work is already done."

The next house we visit is the home of the village weaving group's "fabric banker." She is weaving an open weave, fine cotton scarf alternating white and salmon on a white warp. With Aew's help, we clarify that another group member acts as the microcredit "banker" for the revolving savings and credit program that the weaving and spinning groups in the village have established with Pattanarak's help. We had discussed the group, its numbers, practices, products and history during our drive to the village this morning, so much of what we were seeing is an illustration of those discussions. Nonetheless, the reality is both more complex and more poignant.
The 4 of us go inside her home, while a half-dozen neighbours, extended family and/or group members gather on the outdoor sitting platform, constructed in the more traditional manner: hardwood boards supported by posts that had been dug into the hard-packed earth. While we look at the weaving stored higgly-piggly in a glass cabinet inside, someone comes in and hands our hostess a large toddler who is clearly ready for a pre-nap lunch.

While she nurses, we examine the various pieces. Aew occasionally translates our comments and preferences; our recommendations are noted, as the purpose of this visit is to help the weavers better understand market preferences. Eventually, we choose several dozen pieces. As is my habit, I fold everything, whether or not selected, to a standard size to fit the cabinet. When we are finished and a bill reckoned, the woman thanks me, through Aew, for putting everything back so neatly. Ellen explains that it's a habit that I'd acquired as a child from my father who had sold shirts for a living. This explanation is entirely appropriate, I thought, for people who, until recently, learned almost everything from their parents, beginning at a young age when play and work were not yet differentiated.
"Never mind," I said in the local dialect. "You don't have any free time," I added as I motioned to the weaving bank, the child in her lap, the loom outside the door. Her broad smile seemed to show that she had understood and appreciated my comment as well as my compulsive tidying.
We leave our purchases behind, along with a promise to return, and walk over to the next member's house. Aew explains that most of the members are out in the fields farming today, so our visit will be a little shorter. Perhaps they had forgotten our scheduled visit or maybe they considered bringing in their cassava harvest more important. Regardless, we were not offended. There were enough members at home with very young children, as well as those too old or infirm to do the heavy work that cassava requires.
Our next stop apparently falls into the latter category. Under the house, on the ubiquitous sitting platform, are 2 elderly women, lying down but not quite asleep. The various small tools and the mouths of the 2 women attest to the betel chewing session in progress.

We are introduced to the elder of the 2 women who is extremely hard of hearing and, from the look of her milky eyes, sight impaired as well. Aew explains that these days she mostly spins cotton and leaves the weaving to her daughter, but that she is a master weaver of
khit. As if the woman understood Aew's explanation, she rises and sits at the loom where a tablecloth is in progress. Despite her obviously failing eyesight, the number of bobbins involved and the width of the piece, she proceeds to weave several rows while Ellen, having asked permission to photograph, puts her camera on video record. "Got it," she grins.
After her demonstration, she resumes her place on the platform with her companion. With Aew's help, we piece together their history, despite the difficulty posed by women who either can't remember, can't count or don't consider important, the numbers involved in their personal histories. They are sisters, maybe literally, maybe figuratively. Regardless, they are 6 years apart in age and came over the river together from Laos to Thailand to marry Thai men in this village. It's likely that they were 14 and 20 years of age at the time and that was about 40 or 50 years ago. Many of the women in the village are originally from Laos. This program builds on skills acquired long ago, as most of the women learned to weave from their mothers when they were about 10 years old.
Since the group began in the village 15 years ago, many of these women have received additional training in spinning, natural dyeing, weaving and/or product design from other rural weavers participating in similar groups in several of the neighbouring provinces. Each of the groups has access to somewhat different plants and qualities of water, so dyeing is often an experiment, regardless of the experience of the dyer. This woman had apparently helped train not only her daughter but others in
khit weaving, before she retired to her spinning wheel, a process so well known by her hands that vision was unimportant.

Again, we take our leave and return to the home of the "fabric bank" member, where we pick up our purchases. While we'd been gone, her husband had twisted the fringes on 9 shawls we'd chosen, which had been unfinished only 45 minutes ago. He was not the only man we saw engaged in fibre work, although all of the weaving groups' members are women; Ellen and I had both remarked earlier at the complex and fine fishing gear being netted by another man in the village.
After a full morning, despite the exodus of most of the village to their cassava fields, we retired to the general store/restaurant where we encountered staff (perhaps the entire staff) of the adjacent school, easily identified by their crisp, military-like uniforms. The principal made it his responsibility to formally welcome us to the village as well as interview us in his better than rudimentary English. Before we left, he presented us with 5 kilos of yams, recently harvested.
Our daily life is always curious here, especially because of the juxtaposition of unlikely events. As if to illustrate my point, the eldery sisters walk by with towels on their heads, to protect from the mid-day sun, digging sticks in hand. They are off to their cotton fields where they, along with villagers in 5 counties on the banks of the Mekong, produce more than 2,000 kilos of organic cotton bolls per season.
This is what community development and poverty reduction looks like up close, along the banks of the Mekong, across the river from Laos. Buying from these rural women's groups meets our definition of fair trade and we are grateful for Pattanarak's help in introducing us to these women and working with us on special orders we design together for our Canadian market.

We hope you'll take a close look at the tablecloths, placemats, indigo jackets, scarves, bags and even cotton elephants we bring back and see the diligence, perserverance and life skills woven into every one.
Pii Plaa (aka Alleson)
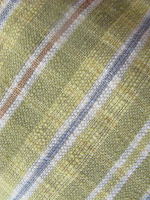
